Parts of Undercarriage
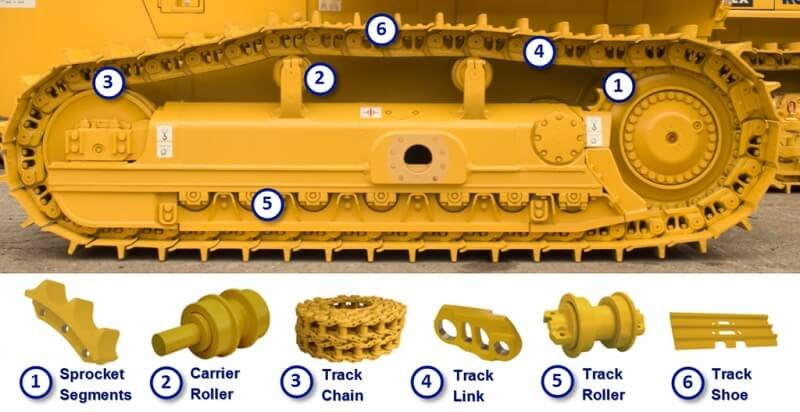
Parts of Undercarriage
The undercarriage is a critical component of vehicles and machinery, particularly those designed for rugged terrains or heavy-duty operations. It refers to the structural assembly located beneath the body of the vehicle, responsible for supporting its weight, enabling movement, and ensuring stability. This system is essential for vehicles such as tanks, bulldozers, excavators, and trucks operating in demanding environments. The undercarriage typically includes components like tracks, wheels, suspension systems, bogie assemblies, idler wheels, drive sprockets, and track rollers. Each part plays a unique role in allowing smooth operation, absorbing shocks, and distributing the vehicle's weight evenly across the surface it travels on.
When discussing the parts of an undercarriage, it’s important to recognize that these components are not standalone entities but rather work together as a cohesive unit. For example, the interaction between the tracks and wheels ensures efficient propulsion, while the suspension system absorbs shocks and vibrations to protect both the vehicle and its operator. Understanding how each part contributes to the overall functionality of the undercarriage is crucial for anyone involved in designing, maintaining, or operating such machinery.
The complexity of an undercarriage varies depending on the type of vehicle or equipment it supports. In some cases, it may include advanced engineering features tailored to specific tasks, such as traversing rough terrain or carrying heavy loads. Regardless of the application, the undercarriage remains a vital aspect of any mobile machinery, influencing performance, durability, and longevity. As we delve deeper into this topic, we will explore the various types of undercarriages, their key components, and their roles in ensuring optimal mobility and stability.
What is an Undercarriage
To fully appreciate the importance of the undercarriage, it’s essential to understand what it is and why it matters. At its core, the undercarriage serves as the foundation of a vehicle or machine, providing support and enabling movement. Unlike the visible parts of a vehicle, such as the cabin or engine, the undercarriage operates largely out of sight but plays an indispensable role in the overall functionality of the machinery. Without a well-designed and properly maintained undercarriage, even the most advanced vehicles would struggle to perform effectively, especially in challenging conditions.
Historically, the concept of the undercarriage has evolved significantly over time. Early versions were relatively simple, often consisting of basic wooden or metal structures designed to carry weight and provide rudimentary mobility. However, with advancements in materials science and engineering, modern undercarriages have become highly sophisticated systems capable of handling extreme forces and complex terrains. Today, they are engineered to meet the specific needs of various industries, from construction and mining to military applications.
The primary function of an undercarriage is to facilitate movement while maintaining stability. This involves several critical tasks, including distributing the vehicle's weight evenly across the ground, absorbing shocks and vibrations, and ensuring traction on different surfaces. Depending on the design, an undercarriage can either use tracks (as seen in tanks and bulldozers) or wheels (common in trucks and loaders). Both configurations have their advantages and are chosen based on the intended use of the machinery.
Why Is the Undercarriage Important?
The importance of the undercarriage cannot be overstated. It directly impacts the performance, efficiency, and lifespan of the vehicle. A poorly designed or neglected undercarriage can lead to numerous issues, such as increased wear and tear, reduced traction, and compromised stability. These problems can result in downtime, higher maintenance costs, and even safety hazards for operators. On the other hand, a well-maintained undercarriage ensures smoother operation, better fuel efficiency, and extended service life for the machinery.
In addition to its functional benefits, the undercarriage also plays a significant role in determining the versatility of a vehicle. Machinery equipped with advanced undercarriage systems can operate efficiently in diverse environments, from muddy fields to rocky mountainsides. This adaptability makes the undercarriage a key factor in the success of many industrial and military operations.
Finally, understanding the undercarriage is crucial for anyone involved in the procurement, maintenance, or operation of heavy machinery. Whether you’re a mechanic, engineer, or operator, knowing how the undercarriage works and what it requires to function optimally can help you make informed decisions that enhance the overall performance of the equipment.
Types of Undercarriages
Undercarriages come in various forms, each tailored to specific applications and terrains. Broadly speaking, they can be categorized into two main types: tracked undercarriages and wheeled undercarriages. Each type has its own set of advantages and disadvantages, making them suitable for different scenarios.
Tracked Undercarriages
Tracked undercarriages are commonly found in vehicles designed for off-road use, such as tanks, bulldozers, and excavators. These systems utilize continuous tracks instead of wheels, providing superior traction and weight distribution on soft or uneven surfaces. The tracks consist of interconnected metal links that wrap around a series of wheels and rollers, allowing the vehicle to move smoothly over obstacles and maintain stability on challenging terrains.
One of the key benefits of tracked undercarriages is their ability to distribute the vehicle's weight evenly across a larger surface area. This reduces ground pressure, minimizing the risk of sinking into soft soils or damaging delicate surfaces. Additionally, the continuous contact between the tracks and the ground ensures consistent traction, even on slippery or uneven surfaces. However, tracked systems tend to be heavier and more complex than wheeled alternatives, requiring more frequent maintenance and repairs.
Wheeled Undercarriages
Wheeled undercarriages, on the other hand, are typically used in vehicles designed for paved roads or relatively flat terrains. Examples include trucks, loaders, and certain types of agricultural machinery. These systems rely on traditional wheels mounted on axles, offering greater speed and agility compared to tracked systems. Wheeled undercarriages are generally lighter, simpler, and easier to maintain, making them ideal for applications where road travel is the primary focus.
Despite their advantages, wheeled undercarriages have limitations when it comes to off-road performance. They tend to exert higher ground pressure due to the smaller contact area of the tires, which can cause them to sink into soft soils or lose traction on uneven surfaces. To mitigate these issues, some wheeled vehicles incorporate specialized tire designs or suspension systems that improve their ability to handle rough terrains.
Hybrid Systems
In recent years, hybrid undercarriage systems have emerged as a compromise between tracked and wheeled designs. These systems combine elements of both configurations, offering improved versatility and performance across a wider range of terrains. For example, some hybrid systems use inflatable tracks that can be adjusted to optimize ground pressure and traction, while others employ articulated joints to enhance maneuverability. While hybrid undercarriages offer significant advantages, they also introduce additional complexity and cost, making them less common than traditional designs.
Understanding the differences between these types of undercarriages is essential for selecting the right system for a given application. Factors such as terrain type, vehicle weight, and operational requirements should all be considered when making this decision. By choosing the appropriate undercarriage, operators can ensure optimal performance and longevity for their machinery.
Key Components Overview
The undercarriage is composed of several key components, each playing a vital role in its overall functionality. These parts work together seamlessly to enable movement, absorb shocks, and distribute weight. Below is a detailed overview of the most important components found in typical undercarriage systems:
Tracks and Wheels
Tracks and wheels are perhaps the most recognizable components of an undercarriage. In tracked systems, the tracks consist of interlocking metal or rubber segments that form a continuous loop around a series of wheels and rollers. These tracks provide superior traction and weight distribution, making them ideal for off-road applications. In wheeled systems, traditional tires mounted on axles serve as the primary means of propulsion, offering greater speed and agility on paved surfaces.
Both tracks and wheels require regular maintenance to ensure optimal performance. This includes inspecting for signs of wear, checking alignment, and lubricating moving parts. Proper care can significantly extend the lifespan of these components and reduce the likelihood of costly repairs.
Suspension Systems
Suspension systems are another critical component of the undercarriage, responsible for absorbing shocks and vibrations generated during operation. These systems typically consist of springs, shock absorbers, and hydraulic cylinders that work together to cushion the vehicle and protect its internal components. Effective suspension is essential for maintaining stability and comfort, especially in demanding environments where rough terrains are common.
Modern suspension systems often incorporate advanced technologies, such as electronic sensors and adaptive controls, to further enhance performance. These innovations allow the suspension to adjust automatically to changing conditions, improving ride quality and reducing fatigue for operators.
Bogie Assemblies
Bogie assemblies are specialized frameworks that support the wheels or rollers in tracked undercarriages. These assemblies are designed to pivot and flex, allowing the vehicle to navigate uneven surfaces without losing contact with the ground. By maintaining constant engagement between the tracks and the terrain, bogie assemblies contribute to improved traction and stability.
Regular inspection and maintenance of bogie assemblies are crucial for preventing failures that could compromise the vehicle's mobility. This includes checking for loose bolts, worn bushings, and misaligned components, as well as ensuring proper lubrication of all moving parts.
Tracks and Wheels System
The tracks and wheels system is one of the defining features of an undercarriage, dictating how the vehicle interacts with the ground. Whether using tracks or wheels, this system is responsible for converting the power generated by the engine into forward motion while ensuring stable and controlled movement. Understanding the intricacies of this system is essential for maximizing the performance and durability of the machinery.
Tracks: The Backbone of Off-Road Performance
Tracks are the hallmark of vehicles designed for rugged terrains, providing unparalleled traction and weight distribution. Each track consists of multiple interconnected segments, often made from durable materials such as steel or reinforced rubber. These segments form a continuous loop that wraps around a series of wheels and rollers, allowing the vehicle to move smoothly over obstacles and maintain stability on uneven surfaces.
One of the key advantages of tracks is their ability to distribute the vehicle's weight across a larger surface area. This reduces ground pressure, minimizing the risk of sinking into soft soils or damaging delicate surfaces. Additionally, the continuous contact between the tracks and the ground ensures consistent traction, even on slippery or uneven surfaces. However, tracks are generally heavier and more complex than wheels, requiring more frequent maintenance and repairs.
Wheels: Speed and Agility on Paved Roads
Wheels, on the other hand, are the preferred choice for vehicles designed for paved roads or relatively flat terrains. These systems rely on traditional tires mounted on axles, offering greater speed and agility compared to tracked systems. Modern tires are engineered with advanced tread patterns and materials to optimize grip, durability, and fuel efficiency, making them ideal for applications where road travel is the primary focus.
Despite their advantages, wheels have limitations when it comes to off-road performance. They tend to exert higher ground pressure due to the smaller contact area of the tires, which can cause them to sink into soft soils or lose traction on uneven surfaces. To address these challenges, some wheeled vehicles incorporate specialized tire designs, such as low-pressure or all-terrain tires, that enhance their ability to handle rough terrains.
Maintenance Tips for Tracks and Wheels
Proper maintenance is critical for ensuring the longevity and reliability of the tracks and wheels system. Below is a checklist of actionable steps to follow:
- Inspect regularly: Check for signs of wear, such as cracks, tears, or uneven tread patterns, and replace damaged components promptly.
- Check alignment: Ensure that the tracks or wheels are properly aligned to prevent uneven wear and reduce stress on other components.
- Lubricate moving parts: Apply the recommended lubricants to all bearings, joints, and other moving parts to minimize friction and prolong their lifespan.
- Monitor pressure: For wheeled systems, maintain the correct tire pressure to optimize performance and prevent blowouts.
- Clean thoroughly: Remove dirt, debris, and contaminants from the tracks or wheels after each use to prevent damage and corrosion.
By following these steps, operators can ensure that their tracks and wheels remain in top condition, ready to tackle any challenge.
Suspension Systems Explained
Suspension systems are an integral part of the undercarriage, tasked with absorbing shocks and vibrations generated during operation. These systems play a crucial role in maintaining stability and protecting the vehicle's internal components from damage caused by rough terrains. Understanding how suspension systems work and how to maintain them is essential for anyone involved in the operation or maintenance of heavy machinery.
How Suspension Systems Work
At its simplest, a suspension system consists of springs, shock absorbers, and hydraulic cylinders that work together to cushion the vehicle and protect its internal components. When the vehicle encounters an obstacle or uneven surface, the suspension absorbs the impact, preventing it from being transferred to the rest of the machinery. This process helps maintain stability, improves ride quality, and reduces fatigue for operators.
Modern suspension systems often incorporate advanced technologies, such as electronic sensors and adaptive controls, to further enhance performance. These innovations allow the suspension to adjust automatically to changing conditions, improving ride quality and reducing wear on other components. For example, some systems can stiffen the suspension during high-speed travel to improve handling or soften it during slow-speed maneuvers to enhance comfort.
Common Types of Suspension Systems
There are several types of suspension systems used in undercarriages, each with its own set of advantages and disadvantages. Some of the most common types include:
- Leaf Spring Suspension: Consists of multiple layers of steel plates stacked together to form a flexible yet robust structure. Widely used in trucks and trailers due to its simplicity and durability.
- Coil Spring Suspension: Utilizes coiled metal springs to absorb shocks and vibrations. Offers smoother performance than leaf springs but is generally more expensive and complex.
- Air Suspension: Uses air-filled bladders instead of traditional springs, providing adjustable ride height and improved load-carrying capacity. Often found in luxury vehicles and heavy-duty trucks.
Maintenance Checklist for Suspension Systems
To keep suspension systems functioning optimally, regular maintenance is essential. Below is a detailed checklist of steps to follow:
- Inspect for damage: Look for signs of wear, corrosion, or leaks in the springs, shock absorbers, and hydraulic cylinders. Replace damaged components promptly to prevent further issues.
- Check fluid levels: Ensure that all hydraulic systems are adequately filled with the recommended fluids. Low fluid levels can lead to overheating and premature failure.
- Test functionality: Perform regular tests to verify that the suspension is working correctly. This may involve bouncing the vehicle or checking for unusual noises during operation.
- Lubricate moving parts: Apply the recommended lubricants to all bearings, joints, and other moving parts to minimize friction and prolong their lifespan.
- Follow manufacturer guidelines: Adhere to the manufacturer's recommendations for maintenance intervals and procedures to ensure optimal performance and longevity.
By adhering to this checklist, operators can ensure that their suspension systems remain in excellent condition, ready to handle whatever challenges lie ahead.
This article continues with detailed sections on Bogie Assemblies Function, Idler Wheels Role, Drive Sprockets Details, Track Rollers Importance, Weight Distribution Mechanism, Mobility and Stability Features, Maintenance of Undercarriage Parts, Common Issues and Solutions, Undercarriage in Different Vehicles, and Impact on Terrain Performance, each expanding on the complexities and practical considerations of undercarriage systems.
Deja una respuesta